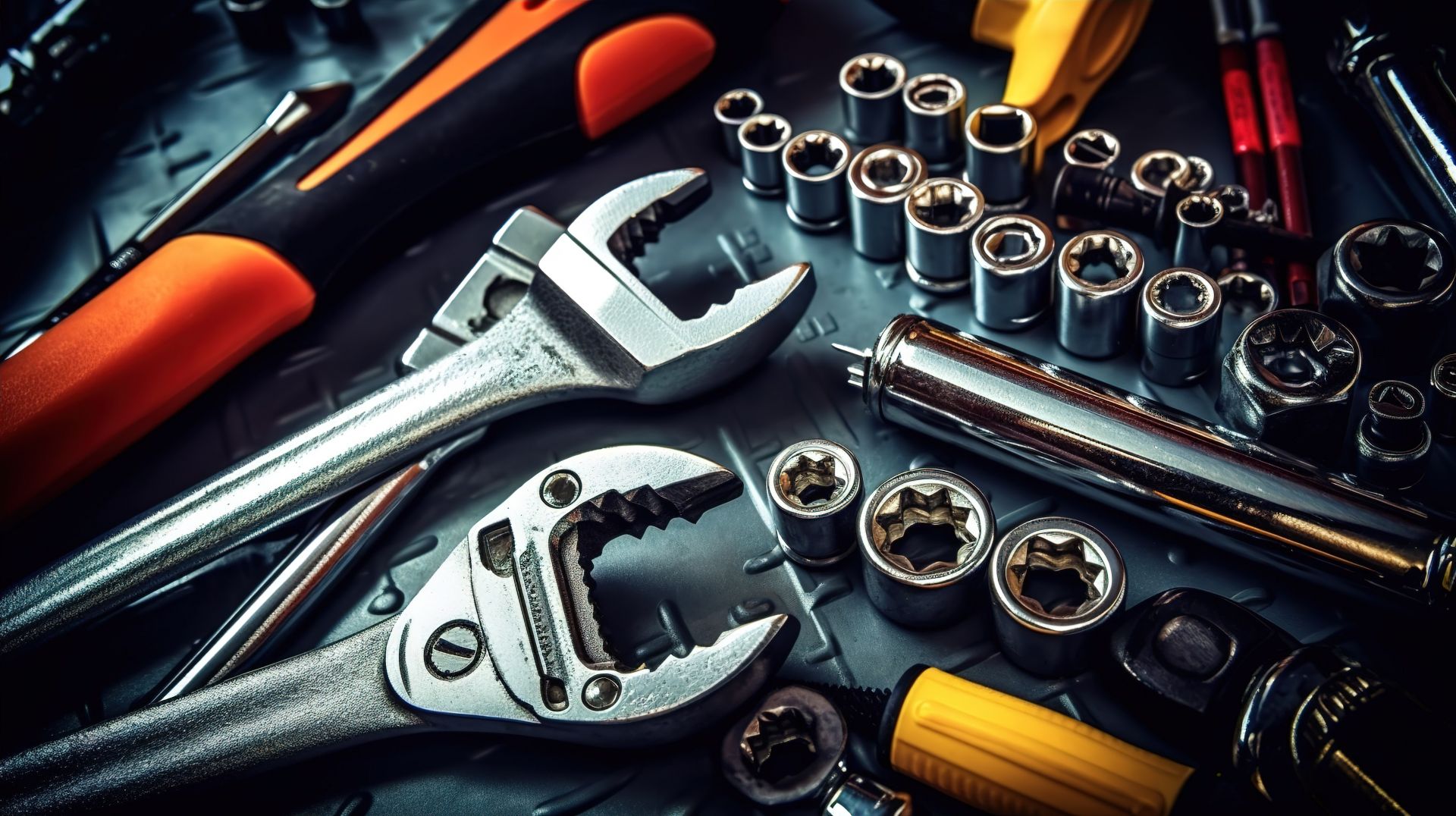
[Customer Pain Points]
A well-known international hand tool manufacturer located in an industrial park in Tainan specializes in producing hand tools of various sizes. The production line uses laser marking processes for identification. Originally, it was a one-operator-one-machine setup, making production capacity and quality difficult to control. Labor issues intensified during the pandemic. However, this mode now faces challenges, with labor costs continuously rising and recruitment of suitable talent becoming increasingly difficult.
[Solution]
Under the planning and design of the ZB Laser team, the single workstation was automated. The vibration bowl laser marking machine was adopted for automatic feeding, combined with visual recognition for material identification and confirmation. After laser marking, the system automatically unloads the materials. Now, the operator only needs to perform one-time loading and unloading, completing the entire laser marking workflow. One operator can manage multiple machines. This change not only reduces labor requirements but also ensures stable production capacity.
This is not just an internal factory improvement but a technological revolution in the industry. This successful case brings new thinking to the hand tool equipment sector, demonstrating the advantages of technology in improving production efficiency and reducing costs.
Keywords: Hand tool laser engraving machine, customized laser equipment, automated laser, hardware parts laser engraving machine