近年來電動車與相關產業逐漸受到重視,也逐漸成為汽車產業的發展方向,這歸因於關鍵的鋰離子電池技術突破。鋰離子電池的製造在手機行業早已成熟,然而電池製造商必須調整製程以趕上日益增加的電動汽車產能,同時確保電池的品質和穩定。雷射加工成為此處的關鍵技術,雷射切割、銲接與打標已經進入電池業的生產線服役。
下圖是電池製造的流程圖。做為原料的鋁箔或銅箔經過鍍膜並壓縮成為電極箔片原料,再經過裁切成電極形狀,銅箔和鋁箔分別成為陽極和陰極。接下來將電極片銲接連結,這裡需要將薄金屬片以搭接(Lap)銲接接合,包含銅與銅、鋁和鋁,甚至銅和鋁銲接,這是一項挑戰。接著將電極薄片包入外殼,成為電池單元(Cell),這裡要將外殼密封,最後注入電解液。由於殼內已經有電極片零件,外殼的銲接不能有太大的熱量避免內部損壞。最後一步是將數個單元組合成電池模組(Module),甚至數個模組結合,這裡需要將單元或模組的電極用銲接串接成導電通路。

▲ 鋰離子電池的製造流程。圖片來源:https://ieeexplore.ieee.org/
【電極箔片切割】
箔片切割成電極,要求切口邊緣不能有顆粒或毛邊,表面的膜層不能有刮損或裂紋,因此切割箔片是非常精細的步驟;另外,為了保持生產效率,某些單位甚至要求切割速度超過50 m/min。要實現這種嚴格且精密的加工,機械切割會有刀具磨損和加工變形的問題,雷射切割是最佳選擇。非接觸式的雷射切割可做到最少切屑損耗、最少變形(包含機械扭曲和熱變形)以及最平滑切口,可以實現靈活加工和高生產率。
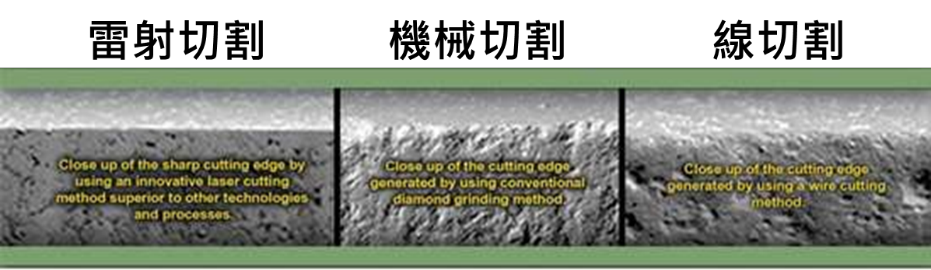
▲ 三種切割法的切口比較。圖片來源:moldmakingtechnology.com
【電極的銲接】
電極材料是銅箔和鋁箔,要將電極永久接合必須以搭接型式銲接,這代表必須做銅-銅、鋁-鋁或者銅-鋁的搭接銲。搭接銲是將上下兩片材料接合,不能在界面有氣孔或裂紋,對於電極而言還要注意接合處的電阻不能太高,否則會增加電能損耗;同時,鋁是不容易銲接的材料,除了活性大易氧化問題,鋁和銅銲接還有脆性化合物生成,容易使接合處裂開,可見電極的搭接銲接是另一項嚴格考驗。
雷射銲接是電極片搭接銲的最佳解決方案:以振鏡式光纖雷射銲接能夠以每秒鐘數百甚至數千mm的銲接速度,快速準確接合電極箔片;脈衝式雷射可以大幅降低銲接熱量,改善電極片變形問題,同時縮短鋁和銅的熔化時間,減少接合點的脆性物質生成,確保銲接處有足夠的機械強度以及降低電阻。此外,銲接路徑還能選擇線性路徑或搖擺路徑增加銲接寬度。要解決電極箔片的銲接困難,雷射銲接是最佳的選擇。
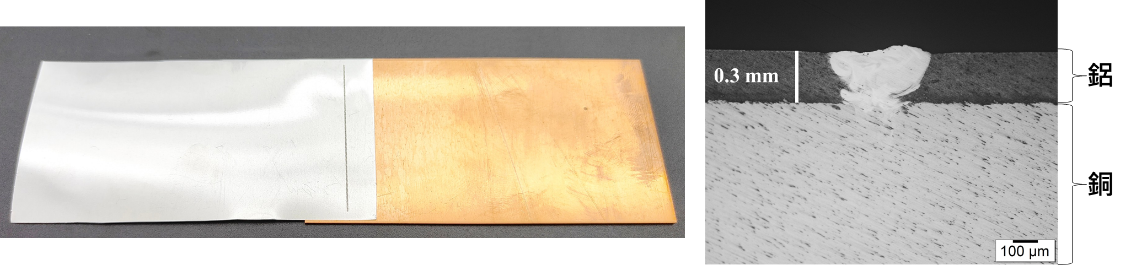
▲ 鋁-銅片以雷射搭接銲的外觀和銲道截面。圖片來源:正鉑雷射
【電池外殼銲接】
電池單元的外殼必須密封,對銲道品質有嚴格要求,此外,由於殼中已裝入電極等部件,銲接外殼的熱輸入要非常低避免內部損傷。因此,可以快速銲接、又具有小的熔化範圍的雷射銲接製程是這個步驟的理想工具,雷射銲道表面平滑,寬度細小又能有足夠的接合強度,由於雷射光的功率穩定,整個銲道的深度可以很均勻,而且適當的功率不會有貫穿的現象,可以避免殼內組件受損。若搭配振鏡式銲接,可以數秒鐘內快速銲接多個物件而不用移動軸向,加快製作速度。
【電池模塊的串接組裝】
電池生產的最後一步是將電池單元組裝成模塊,或者進一步將模塊串接成電池組,這裡需要用匯流條(Busbar)將各個電極連結,正好是振鏡式雷射銲接發揮所長之處。振鏡式雷射銲接大幅減少銅製匯流排銲接噴濺的機會,可得到接合良好無氣孔的銲點,振鏡控制系統還能設定銲道圖形,以圓形或曲線接合。
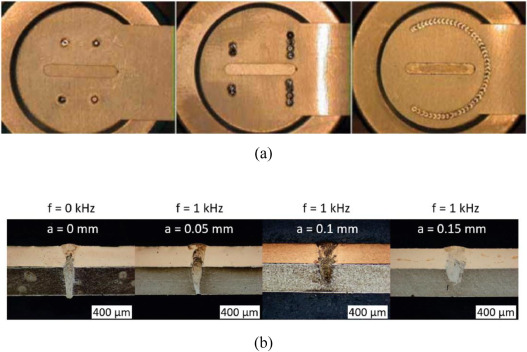
▲ 雷射銲接匯流排,可做不同形狀的銲道。圖片來源:M. F. R. Zwicker, Journal of Advanced Joining Processes
【生產履歷雷射打標標示】
如同許多製造產品要標示生產履歷,用來追蹤該批或個別產品。雷射打標是最適合做生產履歷標示的技術,打標結果不容易被塗改,又能永久保留,而且雷射打標設備可以獨立運作,或者和生產線串聯。
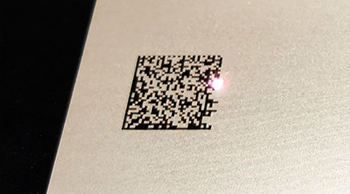
▲ 雷射打標適合電池生產履歷標示。圖片來源:正鉑雷射
好文推薦:
提高生產效率!雷射焊接機優點一一分析給你聽